From Paper to Digital: Transforming Georgia’s Manufacturing Landscape
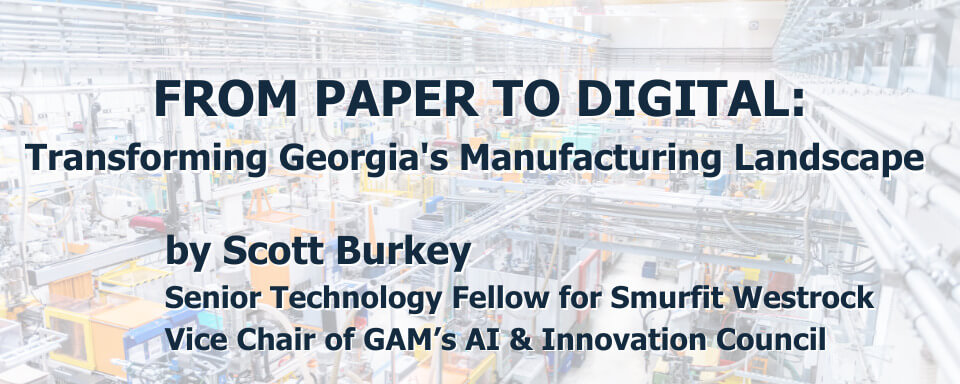
For almost thirty years I’ve worked in technology in Georgia. Beginning in the 1990’s, I worked on some of the largest web and digital properties, like CNN, Coca Cola, and the NBA. In 2019 I had the opportunity to begin looking at how augmented and virtual reality could be used in a global manufacturing company. What I soon discovered is that there is a monumental opportunity for the use of technology in manufacturing and the journey is a wild one with an always-moving target of completion.
Smurfit Westrock operates nearly 600 facilities around the world with over 100,000 employees. Our company, like most manufacturers, operates machines with everything from no cloud connectivity to fully connected machines with all the advancements of such. Thus, our monitoring and analysis of these machines is performed by a myriad of processes, both manual and automated. How we train frontline employees is also done in an assortment of ways. The transition we are going through on our factory floors is happening everywhere and likely happening in your company as well.
Some ways manufacturing companies are shifting from the old ways of operating to digital are:
- Providing digital work instructions on tablets for new hires to utilize during training or to refer to as needed on the shop floor when the trainer isn’t available.
- Installing sensors on machines and pushing data through a gateway to the cloud. Now, you have a way to holistically analyze machine health and production numbers across plants to make data-driven decisions.
- Training on a risky, dangerous, and expensive procedure in virtual reality before the operator performs that procedure on the shop floor the first time.
- 360 virtual tours of a factory are easy to produce and provide real-life experiences of your factory for workforce training, sales, marketing, and customers.
- Remote Assist technology can enable OEM providers to diagnose and resolve machine issues remotely, minimizing delays and downtime.
It seems like a bit of a paradox that I would work for a paper company yet be such an advocate for moving from paper to digital. But the saying is true that, “Paper is where data goes to die.” Once written on a clipboard or printed in a binder, that data (if it’s accurate in the first place) can be lost or outdated within minutes. This paper’s data is also impossible to analyze and act on if not regularly transferred into a piece of software. Switching from paper to digital improves efficiency, accuracy, and productivity in your company.
We all know that fully understanding problems before attempting to apply a solution is of paramount importance. One thing I’ve seen and successfully addressed is a lot of manual recordkeeping that happens on the manufacturing shop floor. Clipboards and three-ring binders, and handwritten instructions are everywhere. The problem here is that the numbers are only as good as the consistency by which they are recorded. Operators get busy and forget to record the entries. Handwriting is often misread. Ink pens get lost. Three-ring binders are sometimes run over by forklifts. You cannot pinch and zoom on pictures on paper or watch videos that resonate with the person looking for vital information.
Training is an aspect of manufacturing that tends to still be handled by antiquated methods in 2025. The new operator on the floor is typically trained by another veteran worker for anywhere from 10 minutes to several days. Most of these veteran workers are great at their jobs but admittedly not adept at effectively training other workers in a way that will resonate with the new operator. Here, we see digital workflows presented on tablets or head-mounted devices beginning to provide portable training assets that the newer “Gen Z” workers are more likely to utilize and understand.
With moving from clipboards to tablets and in-person assessments to digital quizzes and skills assessments, we have a huge opportunity for artificial intelligence (AI) to play a role. Monitoring trends over time to identify gaps in knowledge retention and errors can be addressed using AI. We all know that data is key, but being able to analyze and take action based on the data is where the loop is completed. AI gives us a lot of horsepower for this analysis and decision-making.
If you’re like me, you always look at other companies and think how your own company seems to be lagging in the latest technological advancements. Rest assured, it’s a journey we are all on and you can start today and still benefit from digital transformation. Start simple but start. It is also essential to have a network of peers with whom you can exchange ideas, observe their use of technology, and receive encouragement. The Georgia Association of Manufacturers (GAM) has a lot of resources, and the members engaged in our many councils are here to share their experiences and learnings. I recently heard the acronym “FAIL” stands for First Attempt in Learning. Today may be the day to start small, try something out, and FAIL. I encourage you to be a part of the GAM AI & Innovation Council. Please reach out if I can be of assistance.
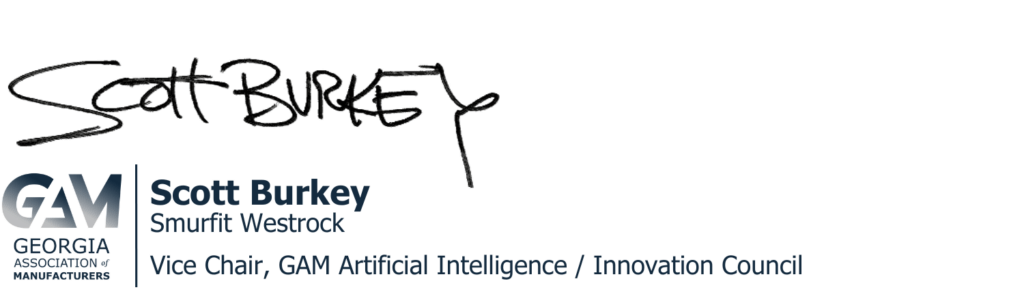